Civil Unions: How the Ironworkers and Carpenters Teamed Up at 7 World Trade Center and Changed the Way We Build
By Matt Chaban September 6, 2011 9:00 pm
reprints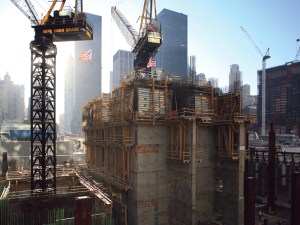
The city’s ironworkers and carpenters have never much gotten along. Falling somewhere between rival sports teams and armies at war, the construction unions responsible for the city’s tall buildings rarely work together—office buildings are made from steel, apartments from concrete (which is poured by the carpenter’s union). “Is there ego? There is certainly pride amongst these unions, and not a little competition,” said Gary Higby director of industry development at the Steel Institute of New York, a trade group.
But 9/11 changed that, or at least the rebuilding of 7 World Trade Center did. It was not simply a matter of camaraderie but also necessity. “Obviously, what you had to do after 9/11 was address the fundamental question of how are we going to create buildings that are as safe as can be in a post-9/11 world,” said Janno Lieber, president of World Trade Center Properties at Silverstein Properties. “The concrete core was probably the single most important of hundreds of safety innovations at 7 World Trade Center that went beyond code. It was a huge step forward for safety and structural robustness.”
It was the invention of the iron-framed building that ushered in skyscrapers 120 years ago. The evolution into steel-framing paved the way for the skyscraper boom of the 1920s and ’30s, the race between the Chrysler and Empire State buildings for pride of place on the skyline, the iconic photo New York Construction Workers Lunching on a Crossbeam.
Construction continued this way in New York for decades, even as the rest of the world has embraced concrete as the ideal material for the core of the walls of commercial buildings. This is because of the efficiency, affordability and flexibility of this hybrid design—steel has to be fabricated and shipped long distances while concrete can be made locally and poured quickly on-site, saving precious months and dollars and allowing for more time for redesigns. Most important of all for 7 World Trade Center, it is much easier to make an unshakeable six-foot-thick wall out of concrete than steel.
But the entrenchment—and a measure of xenophobia—on the part of the construction unions kept concrete to a minimum in New York’s office market. The ironworkers tended to be old-timers, their unions run by Irish and Italian immigrants and their descendents. The carpenters and concrete workers were newer arrivals, from the Caribbean and Eastern Europe. Because a concrete core typically rises ahead of the steel frame, “there was a feeling it was dangerous, that they might drop shit on you, especially if there was a disagreement on the site the day before,” one construction manager said. In addition, there was the perception that it would rob the ironworkers of jobs.
Silverstein Properties managed to achieve a ground-breaking agreement for the unions to work together on 7 World Trade Center. “We’ve been talking about this kind of partnership for a long time, but it was 9/11 finally brought all the sides together,“ said Kenneth Lewis, the project manager at SOM, the firm that designed 7 World Trade.
The concrete core and the steel frame would essentially rise simultaneously, as though one building were being built inside another. It was technologically strenuous work, but from a security standpoint, essential. Not only were the stairs encased in the hardened core, but so too were the communications and climate control systems. “All the essential infrastructure you would need in the event of an emergency is protected by the core,” Mr. Lieber said. This would not necessarily prevent another catastrophe like 9/11, but it would help occupants escape in such an event. The safety of the building was even a factor in the marketing of the building to prospective tenants.
“Buildings that achieve high aspirations are ‘game-changers’ making possible and, perhaps, inevitable, what comes after,” said Rick Bell, president of the American Institute of Architects New York chapter.
Since then, almost every new office building in New York has capitalized on the concrete core, from the Time Warner Center to Goldman Sachs’ new headquarters, the Bloomberg Building to, of course, 1 World Trade Center. “The unions are just doing stellar work together,” Mr. Lewis said. Their partnership has progressed so far that at 11 Times Square and now Tower 3 at the World Trade Center, the concrete cores come first, with the steel frame rising after it, bringing New York up to the international standard.
For all the talk of unity, of the city and the country and the world coming together in the wake of 9/11, it is nice to know that, with much of that fractured over the past decade, at least the city’s hard hats are still getting along.