Breaking Down Deal Breakers in Office-To-Lab Conversions
By Anna Staropoli September 22, 2022 8:05 am
reprints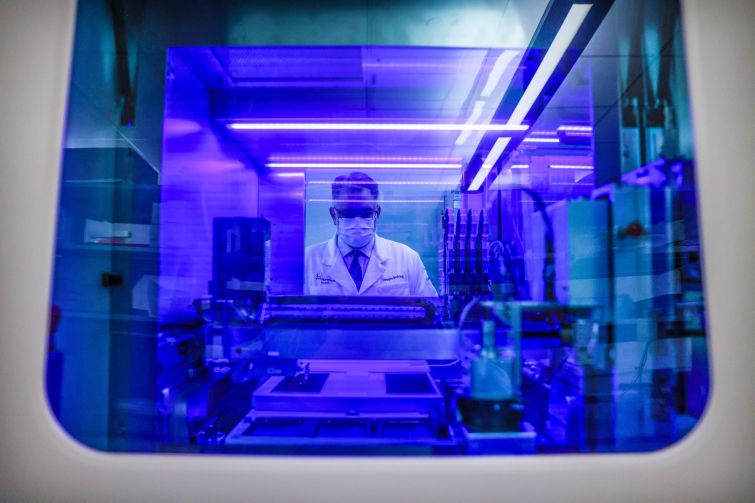
Creativity and scientific research are typically at odds; one is all right brain, the other stays left. Yet when it comes to creating life sciences development, both are on the brain. For a lab to analyze data, run experiments and assess the results, developers must think outside the box and consider many features beyond the standards of office buildings.
“The needs for the tenants are different than just a classic [office] — a journalist or public relations firm — because it’s very heavy in electric need, in venting and in expansion space,” said Leslie Himmel, a managing partner at development firm Himmel + Meringoff Properties.
In 2005, Himmel + Meringoff purchased 525 West 57th Street, which currently houses life sciences tenants such as LabCorp, a company specializing in diagnostic testing and drug development. For the last 17 years, Himmel + Meringoff has navigated life sciences development, though back when Himmel first started, the industry had yet to establish that title. Now, as more money and attention fuel the industry, life sciences has gained traction. With that momentum comes demand and a need for buildings to deliver.
To meet the growth of life sciences tenants, developers have widely adopted the strategy of adaptive reuse. Depending on the building, some aspects of offices easily lend themselves to labs, while others can be amended to fit tenant needs.
“What has made the rehab so attractive is kind of the speed-to-market proposition, where those buildings can get converted more quickly than permitting and going through a construction process for a new building,” said John Sullivan, president at architecture firm SGA.
SGA deals with new construction more than it does building repositioning, though tenant demand has driven an increase in adaptive reuse. But the process of converting buildings into science-specific spaces is not without its challenges. Certain structural features remain must-haves for life sciences, so developers, design teams and the like must come up with creative solutions to convert standard buildings into laboratories capable of cutting-edge research.
“The No. 1 thing that people talk about is floor height,” said Matt Haverty, head of construction at Oxford Properties. “That is primarily due to the fact that there are fresh air requirements for labs that require you to turn over the air and have new air — not recirculated [air], which is what the 95 percent of office buildings use.”
Because labs require new air, they need more and larger duct runs, Haverty said. These take up more space in the ceiling, so floor-to-ceiling heights and the amount of space between floors are primary indicators of whether a building has the potential to become a lab at all.
“There’s usually a volume between the ceiling and then the next floor above,” Sullivan said, “and that’s where you need to solve for all of the duct work and for all of the structure and all of the infrastructure needs for the space.”
As for the specifics of these heights, the taller, the better, said Himmel, setting 10 feet as a rough baseline for ceiling heights. For total floor-to-floor heights, architecture firm Gensler sets a higher range of 14 to 16 feet, while SGA points to 14 feet, 6 inches as the golden measurement.
“What’s driving that [number] is an acceptable ceiling height in the market, which is at around 10 feet,” said Sullivan, echoing Himmel’s estimate. “So above that 10-foot threshold, there’s a considerable amount of duct work, there’s structure, there’s lighting, there’s piping. And that all needs to fit within the remainder of that dimension that makes up that 14 feet, 6 inches. So we find anything lower than that pushes that 10-foot ceiling down with it.”
To truly understand how ceiling and floor-to-floor heights impede adaptive reuse, look at New York City’s streets. New York has all the right features for life sciences progress, like access to hospitals and academic institutions. Yet many smaller offices, as well as side street buildings in Midtown, aren’t up to par with the ceiling heights required for labs, said Himmel. This non-starter brings life science potential to a standstill before it’s even had the chance to be explored.
But while proper ceiling heights enable the circulation of new air, they aren’t the sole way of meeting that need. Rather, there are creative solutions for working around spatial barriers. For example, additional shafts can be built into the ceiling, though this solution presents yet another list of building requirements: namely, roof space and access, as well as the structural capacity for such alterations.
Beyond this alternative, there are even more creative ways to work around low ceiling heights, said Haverty. And although doable, these solutions are not ideal. The give-and-take of lab necessities poses the question of when a building’s original features — or lack thereof — become deal breakers for scientific reuse. Just because you can work around a barrier doesn’t mean you should; at a certain point enough is enough, especially when you want to present the best possible building to your tenant.
Without the right infrastructure, buildings that would be Class A offerings may become Class B on the market, said Sullivan. Architects can attempt to reposition buildings, yet the spaces may ultimately yield lower rent returns and appeal to fewer tenants.
“I think a lot of buildings can’t be converted to life sciences,” Himmel said, noting that venting, extra electricity and generators are among other crucial, technical components a lab must contain.
As such, identifying buildings ideal for the life sciences industry requires plenty of trial and error, critical judgment and patience.
“We’ve looked at a bunch of buildings that you would not want to convert,” said Abby Mondani, director of life sciences, West Coast at Oxford Properties.
Mondani and Haverty estimated they’ve seen roughly 100 buildings within the last two years. While many properties appealed to them, they often couldn’t get past certain key components. Without the right infrastructure — proper ceiling heights, as well as loading capacity and ample column spacing — moving forward is challenging and likely not worth it.
In addition to ceiling heights, Haverty pointed to the freight elevator situation, the location of the loading dock and, if it’s a chemistry lab, access to chemical storage as pivotal conversion considerations. Loading and site access pose significant barriers to a laboratory’s success, not to mention tenant safety.
Another strict requirement for many lab users is the aforementioned column spacing, which immediately helps developers weed out potential lab spaces. Oxford Properties involves a design team early on in assessing a property. Once the space is laid out, it’s easy to see whether it will work for a future lab.
Putting in such legwork is essential in all kinds of development, but in life sciences it’s especially critical. Beyond the bare-bones structural and logistical essentials, lab spaces must account for hyper-specific tenant needs — a task made all the more challenging when you don’t yet know who your tenants might be.
“While we always will engage the local market [and] the experts in the local market to determine the viability of the customer acquisition success, we typically won’t move forward on these projects with a tenant in place,” Mondani said.
Working on spec lends itself to the speed of the life sciences industry. Once labs procure funding, they look for spaces to inhabit. When a life sciences company is just starting out, these spaces can be fairly generic. However, as the company evolves and becomes increasingly specialized, the building must be able to accommodate new specific, technical needs.
“Lab space is not generic,” said Himmel. “It’s very different for a neurology lab than an immunology lab. … They’re doing different things.”
Because much of life sciences development occurs on a speculative basis, developers are building for needs they may not fully understand. While seemingly blind development sounds risky, anticipating building requirements is actually fairly straightforward. Sure, developers can’t necessarily predict a specific tenant, but they can gauge the kind of science best suited to the building’s location.
In the life sciences industry, the concept of clusters often reappears, referring to geographic origins that see set scientific practices. If a building is converted within a specific cluster, that space will likely attract tenants similar to neighboring labs.
“You typically understand the demand of what is the science that is clustering in the market,” Mondani said . She pointed to Seattle — where Oxford recently finished a 130,000-square-foot office-to-lab conversion — as a market focused on cell and gene therapy.
Once companies determine the trends of the market, they can plan their conversions accordingly and predict whether a life sciences company will thrive in any given building. What works for one lab may not work for another. Biology labs, for example, are fairly versatile and capable of operating within chemistry-centric spaces. Yet chemistry companies may not be able to function outside of a chemistry-specific building.
These differences boil down to spatial features that may seem inconsequential but are integral to a lab’s line of work. According to Haverty, sinks are crucial for chemistry labs. Because of the discipline’s routine use of chemicals and liquids, a chemistry company requires a significant number of sinks right from the get-go.
“[Sinks aren’t] something you can easily adapt afterwards,” Haverty said, “because it’s a considerable amount more of the infrastructure: the kind of core and shell components that would need to be altered to allow for that to happen.”
While plumbing, HVAC and electrical requirements may seem more adaptable than, say, ceiling heights, they represent fundamental components of a building. It can be challenging, not to mention expensive and dangerous, to change such infrastructure after the fact. Unless a chemistry tenant isn’t doing much chemistry, a chem-heavy lab would struggle to work in a sink-less space.
You want to understand your infrastructure from day one, recommends Haverty. Once you identify a target tenant, you can cater the conversion and design process to that tenant’s needs — or abandon ship, should the essentials not be in place.
Yet even when the features align and a building seems ready for conversion, a lab doesn’t exist in isolation. Every building comes with a neighborhood, and the location of a company reflects its access to the larger, neighboring cluster of scientific research. For labs looking for inspiration, resources and collaboration, connectivity may be just as important as ceiling heights.
“I think it’s more about the neighborhood,” Himmel said, “and ‘Am I in a cluster where tenants want to be?’”
Anna Staropoli can be reached at astaropoli@commercialobserver.com.