Former Philly Steel Factory Set for Rebirth as Life Sciences Hub
New York firm finds footing with Philadelphia BuddBio site
By David Nusbaum June 29, 2022 5:45 pm
reprints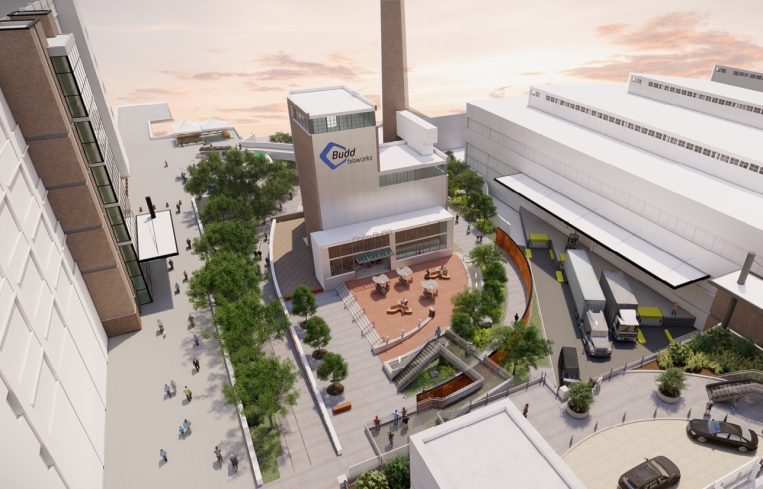
A site that manufactured tanks for World War II is ready to tackle the next generation of global challenges as a bioscience research, development and commercial manufacturing facility.
The long-dormant, 25–acre Budd Companies site in northern Philadelphia was acquired by New York-based Plymouth Group in 2019 for $6.5 million, and the private equity firm has undertaken a major transformation of the property to accommodate pharmaceutical manufacturing.
Although costs were not disclosed, Davis credited its investment partner Centerbridge Partners, which shares the vision for the site. Colliers was hired to handle leasing.
The hospital and university systems in Philadelphia have been significant drivers for life sciences growth thanks to research funding and deep talent pools. However, the scope of operations typically stops at large-scale manufacturing because of a lack of facilities compared to other markets such as Boston and San Diego. The Philadelphia area has one of the largest biotech hubs outside of those markets with 21.3 million square feet of inventory, according to the Colliers Spring 2022 Life Sciences Snapshot.
Because of its historical use, the design features at the BuddBio campus are not typical in most spec developments, and it’s more difficult to redevelop because material costs are generally too high. The buildings have thick foundations, high ceilings and abundant power supply. Moreover, supply chain shortages and delays make it difficult to procure the materials needed for construction and roofing.
“The utility loads are a real impediment to bringing these types of buildings online,” Michael Davis, founding principal of Plymouth Group, told the Commercial Observer. “Our Pioneer building was designed to hold Sherman tanks. The buildings have floor loads and clear heights that work for almost anything.”
Yet the properties were dormant for years since manufacturing shuttered in the early 2000s, and the communities in the surrounding northern Philadelphia area that were supported by warehouse jobs have struggled. Plymouth Group hopes that repositioning these buildings for life sciences will bring a lot of higher paying jobs.
An alternative use could be as a logistics site, but those facilities may not produce as many job opportunities as robotics and automation become increasingly more utilized in warehouse operations. Planning a massive life science operation that can offer growing companies a chance to scale in a major market was something that the local government and industry supported.
“They were the biggest employer when they left,” Davis said. “It can shred a community.”
Although the project has been in the works for several years, Plymouth Group enhanced the property with a key $15 million acquisition in March of an adjacent building on 17 acres that solved parking and transportation needs. With that piece in place, the focus has turned to tenant improvements and leasing agents at Colliers have engaged prospective tenants. The first lease deals are expected to close shortly; manufacturing could begin by the end of the year.
The average asking rent in Philadelphia is at a significant discount to the other major life sciences markets at $54 per square foot compared to $110 per square foot in Boston, $78 per square foot in San Diego and $70 per square foot in the San Francisco Bay Area, per Colliers data.
The initial phase will bring about 1 million square feet online. It could eventually reach upwards of 4 million square feet, making it one of the largest urban life science projects in the country. Tenants can expand on site rather than outgrowing space and needing to relocate.
“People worked hard to figure out how to take millions of feet and make it feel programmatically thoughtful. We may have one of the largest parking lots in the city of Philadelphia now. The challenges we had fell into place with the parking,” Davis said.