Repositioning a Building For Life Science Tenants
By Adam Spagnolo and Brooks Slocum July 6, 2020 4:17 pm
reprints
As the life science sector rapidly advances, the fundamentals of repositioning buildings into life science facilities are evolving as office tenants move away from dense environments. While the scope of renewal can vary widely from building to building, keeping a few important factors in mind can help investors reposition traditional office buildings for life science uses.
Life science real estate is capital intensive. The most economical option for repositioning an existing office building is to start with a typical commercial building that already has finished lobbies, restrooms, elevators, corridors, amenities and loading docks. The work we’re doing on 95 Greene Street in Jersey City is a great example of this option.
Repurposing is a sustainable solution that supports preservation and breathes new life into an old building. Linx, a campus for life science companies in Watertown, MA that SGA is working on, is the adaptive reuse of an underutilized 1980s warehouse building into a campus for science and tech companies.
Among the important considerations in a life science repositioning:
• Envelope: High-performance envelopes are required for lab-use due to higher moisture content. Lab uses can be affected by exterior light within the space.
• Structure: One must establish acceptable access to mechanical and plumbing shafts and risers. New buildings can be planned for locating shafts as needed. In existing buildings it’s important to find appropriate locations for shaft ways based on the existing structural frame. Future slab knock-outs to create new shafts should be pre-planned.
Life science bay spacing is typically on an 11-foot lab bench module, but lab layouts can be flexible to accommodate existing structures. An ideal floor-to-floor height is 14 -and-a-half feet or taller. Lower floor-to-floor heights require site-specific solutions for ductwork pathways.
In addition to lab areas needing a higher live load capacity, laboratories also require increased floor loading, stiffness, and vibration. Lab floor loading is typically 150 pounds per square foot and may require up to 200 pounds per square foot for specialized equipment locations. Typical office buildings are designed to limit floor vibrations to 4,000 MIPS (micro inches per second) and labs using sensitive 400X magnification scopes may require a structural frame with vibrations at or less than 2,000 MIPS. Typical causes of vibration are long-span structures and transportation infrastructure adjacent to the buildings.
• Core and Shafts: Lab-ready bays with available core space that can be utilized for future shafts are important. Deciding on what is base-building and what is tenant fit-out is important to determine depending on single or multi-tenant floor layouts. Base building shafts are fitted with ductwork that is stubbed out at the shaft wall ready for tenant connections. Tenants may need to access the shafts at time of their construction, which can cause issues with other tenants occupying space near the centralized shafts. Dedicated rooms for PH neutralization systems and process gas storage should be located on ground level for chemical deliveries, storage, and access for maintenance.
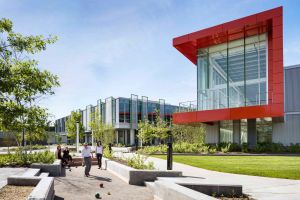
• MEP: Typically, tenants are allocated 10W per square foot for power use, most life science tenants require increased primary electrical service; adding standby power to the base building system requires establishes areas for future standby power generators to be located. A mechanical penthouse or additional rooftop equipment space is necessary (and can be rented) for tenant equipment including stand by generators. Some lab uses require increased water supply and sewer capacity particularly if there is any on-site production in addition to research. Lab exhaust studies may be needed to understand how exhaust plumes affect neighboring areas.
• Ratio of Lab versus Office: Typical life science programs range between 40 percent office and 60 percent lab, to 60 percent office and 40 percent lab. It’s important to determine the mechanical, electrical and plumbing upgrades due to this increase in mechanical requirements for the labs.
• Vivariums: A life science facility with vivariums requires cleanroom spaces with separately controlled conditioning and exhausting systems. In buildings with lobbies, dedicated elevators are needed that open directly into tenant receiving rooms. Containment rules require dedicated screened loading docks for animal delivery and disposal, daily bedding, and food deliveries; enclosed loading is important for tenants with animal control facilities.
• Hazardous Uses: The location of hazardous storage space has code ramifications on fire ratings for structural elements. The height of a building also has special considerations. Highrise construction requires proper control areas and lab units relative to the building’s use and code.
Adam Spagnolo and Brooks Slocum AIA lead the Manhattan office of SGA, the New York City and Boston-based architecture practice.