Robots Are Coming Online to Change Construction Forever
By Liam La Guerre September 20, 2017 7:30 am
reprints
SAM is the construction worker who never takes a break. SAM never gets sick. SAM can lay approximately 100,000 bricks in a single month. Just don’t ask SAM to do corners.
Earlier this year, SAM—or a “semi-automated mason”—showed up at the construction site of Shenandoah University’s new 80,000-square-foot James R. Wilkins Jr. Athletics & Events Center in Winchester, Va.
“It was interesting,” said Donnie Werdebaugh, a 40-year construction vet of the Virginia-based general contractor Howard Shockey & Sons, who, at first, was dumbfounded when the foreman of his project started telling him about the bricklaying robot which looks like a giant refrigerator with a robotic arm and a conveyor belt.
Werdebaugh watched the whole process of brick work change before his eyes as the robot placed nearly 375,000 bricks during the next three months—a job that would have taken one construction worker more than 20 months to do.
“I’ve been on projects [prior] where we didn’t have a robot, and we had a lot of bricks to lay and needed 20 masons, but we only had 15,” Werdebaugh recounted to Commercial Observer. The robot “enhanced manpower, and it enhanced production.”
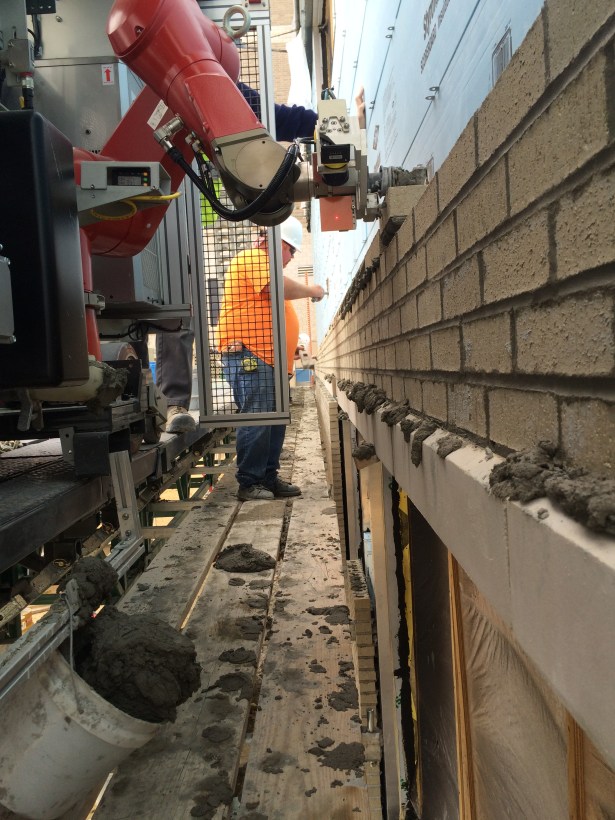
Over the past decade, new companies have been popping up with robotics to handle a myriad of tasks on construction sites from bricklaying to surveying to welding. While various construction management executives and experts with whom CO spoke agreed that the robotics industry is still very nascent in the construction business, the demand is there, and startups are testing more devices all the time.
Construction Robotics, a 20-person startup based in Victor, N.Y., started working on SAM in 2007. After about eight years of development, research, polling and tweaking, it began selling the bot two years ago.
It’s easy to see why SAM is desirable. The machine can lay just over 3,000 bricks a day, more than five times faster than an average human, who can lay between 500 and 600 bricks daily—and it lays bricks perfectly vertical. SAM was so fast on the Shenandoah University job site, it set a world record for the most bricks laid in an eight-hour period at 3,270, according to Construction Robotics’ website. Shenandoah University tweeted about the work and “will continue to partner with [general contractors] to utilize industry trends,” according to Jeff Davis, the university’s physical plant project manager.
Of course, SAM is not yet taking over the construction industry. For starters, there are only 10 of them (five of which have been sold, and the remainder are for rent at an undisclosed amount), according to Rafael Astacio, the director of sales for Construction Robotics. Plus, SAM costs $425,000 (down from the original price of $500,000 two years ago). Also, SAM can’t really work on corners well, Werdebaugh said. A long horizontal surface without protruding items is perfect for it to handle. Coming in at 3,000 pounds, SAM requires a reinforced scaffold to move up and down walls.
Still, the robot has been used across the country on a variety of construction projects, including The Lab School in Washington, D.C., and an Aldi supermarket in Pulaski, N.Y.
Now Construction Robotics is working on its second product, a mini-crane-like arm that would allow a contractor to move heavy blocks of concrete at construction sites. The bot, which should be available for sale by the end of the year, will retail for $65,000 to $70,000.
The demand “is coming because the older generation is moving on and the younger generation is more [accepting of that] that kind of change,” Werdebaugh said. “It is something that took this younger generation.”
One point of pride for the company is that it doesn’t eliminate the need for humans, Astacio said. “The mission of our company is not to replace humans. The main mission is to keep developing this collaborative robot to work alongside the mason and take out the heavy lifting.”
SAM has a conveyor belt of bricks and a robotic arm that grabs the bricks, lathers them with mortar and places them on the wall. Workers are needed to survey the machine and make sure it is working correctly, feed it more bricks and trail the robot’s work to smooth over the concrete.
Not everybody is so sanguine about the impact a bot will have on the business. Of the major New York construction firms that CO contacted for this article, including Skanska, Lendlease, Gilbane Building Company and Hunter Roberts Construction Group, not one agreed to comment. Moreover, labor leaders recognize the damage it can do to its workforce.
“I don’t know much about this subject, but it’s natural to believe that, depending on what work a robot can safely and competently perform, it could reduce the number of people needed on a job site,” said Louis Coletti, the president and chief executive office of the Building Trades Employers’ Association of New York City, which has 27 contractor associations under its wing and represents 1,800 firms. “The construction industry is not immune to the technological revolutions in society. Did anyone ever expect that robots would replace people on auto assembly plant lines? That is what is happening today.”
Indeed, automobile factories have used robots to assemble cars for more than half a century, beginning with Unimate, a robot that was installed in a GM factory in New Jersey for die-casting and welding in 1961. Machines have been used for counting and bottling tablets and capsules since the 1970s and today robots in hospitals and pharmacies around the country pick out medicine and dispenses it after doctors write prescriptions. Companies with massive warehouses, like Amazon, are using bots to move merchandise.
Other bots, besides SAM, are being employed at construction sites nationwide. As part of a pilot program, California-based DPR Construction has tested a robot that does layout work—or sprays the lines and markings at construction sites. These are used at sites so workers know where to precisely install plumbing, mechanical and electrical systems. In YouTube videos, the device looks like a small creature scurrying around for food as it glides across floors of projects doing its job. DPR declined to speak about the bot via a spokeswoman as it was a pilot program.

And for larger projects, like bridges, companies are using robotic welders. Construction workers used bots from Louisiana-based Wilkinson Technologies in 2014 to hasten the installation of 1,000 steel piles to support the new nearly $4 billion Tappan Zee Bridge (renamed the Mario M. Cuomo Bridge) across the Hudson River in Tarrytown, N.Y. A team of contractors oversaw the work of the robots, which can weld twice as fast as humans and reduce defects, as The Journal News reported. The project will be completed in 2018.
A representative from Wilkinson did not return multiple calls from CO for comment.
And construction companies are using drones to get a better view of projects and perform inspections. Drones haven’t quite become mainstream on sites, yet, but the idea is one that makes at least one construction manager in New York City giddy. It could be effectively used to comply with Local Law 11, which requires owners to check exteriors of buildings that are more than six stories every five years.
“Building owners are forced to put an ugly scaffold bridge and drop men from the roof to do an inspection of the façade,” said Ken Colao, the president and founder of construction management firm CNY Group. “With the use of drones, you can have someone standing on the ground, which can do a telescopic analysis of the façade to check for leaks. This can eliminate the sidewalk bridges and putting men on scaffold [if nothing is found in violation].”
Colao’s company has not yet worked on a project that has used the technology, but it has started researching it.
“Our construction industry has not changed since the times of the pyramid,” said Richard Lambeck, the chair of the construction management program at New York University’s Schack Institute of Real Estate. “It’s all done by labor; it’s very labor intensive.”
Lambeck explained that it is easy to create robots for industries where the work produces the same overall product, such as cars. Construction, on the other hand, is usually different for each complete structure and requires greater cognition.
In addition, costs for research and implementation of robots make it currently prohibitive. For there to be new products, subcontractors and general contractors would have had to spend big sums to innovate, Lambeck said. There are tight profit margins on projects for most subcontractors and general contractors, so the thinking is, if it ain’t broken, why fix it? That’s why startups like Construction Robotics are stepping into the void.
And there are more basic reasons why the industry is slow to change. Construction sites are inherently hazardous places—where there are thousands of ways for workers to get hurt—and ceding control to a machine is something that people on all sides of the real estate business are reluctant to do. Plus, there are union rules to contend with.
“New York is dominated by union construction,” said Oscar Vera, a vice president at general contracting company Cauldwell Wingate. “So their union rules would have to evolve or change to adopt new technologies.”
Gary LaBarbera, the president of the Building and Construction Trades Council of Greater New York, which represents more than 100,000 workers wasn’t particularly keen on robots.
“I’ve never seen robots on a New York City construction site, and I don’t see how a robot could ever come close to a well-trained and highly skilled unionized construction worker in New York City,” LaBarbera said in a prepared statement. “You can’t program that kind of heart and real-world experience.”
To date, no developer has contacted the New York City Department of Buildings with an application to use a robot, according to an agency spokesman. And robots are not specifically covered in guidelines for robots on construction sites in Gotham. Any application to use one would have to be reviewed by the DOB, and it would have to follow the same regulations of devices like cranes, hoists and excavators.
Still, there are those who believe the robot’s role in construction is inevitable. By 2050, construction sites will be human-free, according to a report by infrastructure group Balfour Beatty, based in London with U.S. headquarters in Texas. The company predicts robots will work together to complete structures, while drones will tour over sites collecting data and detecting hazards. Humans will remotely manage projects, and they’ll use 3D and, in some cases, 4D printing (models that can change with exposure to heat, sound or moisture) to complete structures faster. In the rare cases that humans visit sites, the report says it will be in an enhanced exoskeleton, and they will use “neural-control technology” to influence robots.
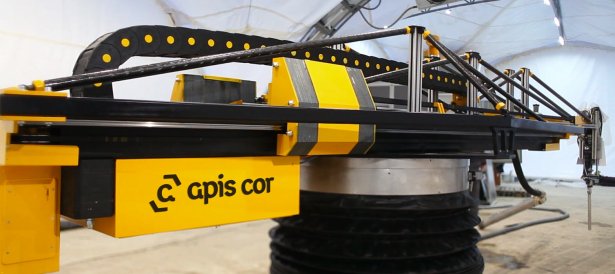
“Over time, the use of robots will become more cost-effective, and we will begin to see a boom in the use of [them] in construction,” according to the report entitled “Innovation 2050 – A Digital Future for the Infrastructure Industry.” “The increasing use of robots on-site will begin in areas involving repetitive tasks. Elsewhere it will take the form of machine-to-machine communication in areas such as remote inspection and remote site visits, or putting together preassembled modules.”
The benefits will include the ability to address the shortage of construction workers around the world. (The construction industry in the U.S. had about 232,000 job openings in July 2017, according to the U.S. Department of Labor’s Bureau of labor Statics report on Sept. 12. That’s a slight improvement from 238,000 job openings a year ago, but still a significant shortage of workers.)
“[Developers] want to build it as cheaply as possible,” Vera said. “The only way to do that is to find new ways to make construction more efficient. I don’t see materials changing drastically over the next half-a-century, but I think there are going to be more robotics—just looking at the history of other heavily labor-intensive industries.”
There may not be much of a wait for that future as companies across the globe are already using giant 3D printers to create homes.
In March, Apis Cor, a San Francisco startup, developed a 3D printer that created a 400-square-foot home for $10,000 in Stupino, Russia, in just one day. The printer resembles a suspension bridge that rotates as it prints the building, as observed in a video of the process.
Oddly, since the Stupino house was built—and the press caught wind of it—the company has gone silent. It stopped posting on its blogs, Facebook site and Twitter account. There isn’t a phone number listed on its website, and no one responded to CO’s multiple requests for comment via email.
Larry Haines, the founder of Houston-based developer Sunconomy, who planned to create small affordable homes with Apis Cor’s technology, said Apis Cors called off its agreement with him. All he knows is the 3D-printing startup fell off the grid, and he heard that it changed its business model. Haines is now working with a small staff to create his own 3D printer so he can stay on course.
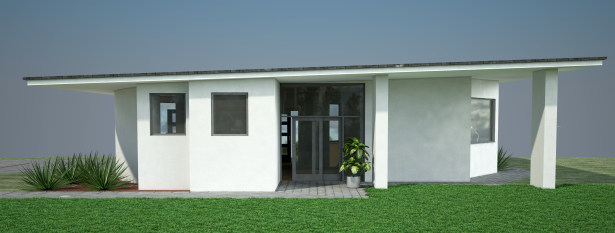
Haines said his device, which should be ready for testing in 90 to 120 days, will be able to produce homes in three days. He envisions using the technology to eventually create close to 5,000 homes a year, which could certainly help solve any affordable housing crisis. He is still researching the “ink” of the 3D-printed homes so they are more fortified than current homes. And he plans to include more efficient systems, such as fire protection, water collection devices and electricity generators, in the final product.
“I want to build a very affordable house that is better that what we have now,” Haines said. “Otherwise, what is the point? I’m trying to build houses that are designed to last for centuries.” Referring to the famous quote by hockey legend Wayne Gretzky, Haines added that he metaphorically hopes to “skate to where the puck is going, not where it has been.”