When Commercial Observer spoke last week with SL Green Realty Corp.’s director of sustainability, Jay Black, Earth Day was fast approaching. But for Mr. Black, 34, every day is Earth Day. Previously a director of architectural services at the company, he succeeded in a mission motivated mainly by “self-enjoyment” to help SL Green become a leading “green” property owner across its Westchester and Fairfield County portfolio. A promotion to his current role in June 2011 allowed him to expand that distinction to the firm’s 70-plus property city portfolio. For Mr. Black, who leads by example when it comes to the environment, there couldn’t have been a more appropriate challenge.
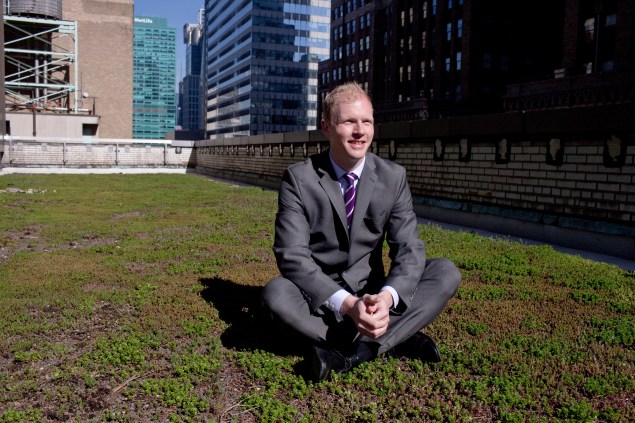
Last month, he spoke at the annual Eco Products International Fair in Taiwan to share his views with the world, but his approach starts at home. He insists that his family buy milk in glass jugs in the same way that he dictates SL Green’s ongoing building retrofits, LED-lighting upgrades and carpet-recycling initiatives. His passion translates into a more efficient portfolio, millions of dollars in savings for the firm—and perhaps fresher milk at home. Mr. Black spoke with CO about his environmental initiatives and philosophies. They might come under the spotlight on Earth Day, but Mr. Black has made them a mainstay of SL Green’s year-round business operations.
How do your firm’s actions fit into the climate change debate?
There is well-documented information suggesting that climate change is happening. There are a lot of different beliefs as to why it’s happening. I like to believe that our efforts to improve environmental standards have a positive impact on the environment that can help mitigate climate change or lessen the impact.
But it’s important to see that these environmental initiatives, regardless of personal viewpoints on climate change, are also a great tool for our business. We want to use sustainability as a driver to make our business better, benefit our company and also have a positive impact on the environment.
In March you spoke at the Eco-Products International Fair, in Taiwan. Why was that event important to you?
It allows us to get involved on the international stage and share our message with organizations from various countries, and to help provide a possible blueprint for others to follow. In many ways, Asia [and America] share very similar sustainability concerns and issues in terms of improving efficiency standards, water conservation and recycling. Given their increasing interest in those initiatives, I think it’s important to stay connected and share best practices so we’re all collectively improving what we’re doing.
How does your intrinsic passion for environmental issues translate into your work?
My family and I make every effort to implement best practices and to try to be as efficient as possible, upgrading our home with more efficient appliances and insulation. And we now have milk delivered to our house that comes in glass bottles that are picked up and reused to reduce waste. Also, we buy things from a local source. That sentiment and desire to be part of the positive change carries over into what I do in the business. Buildings are such a large user of energy and contribute so much to waste generation and water consumption. Working for a company as significant as SL Green here in the New York City marketplace gives me an enormous opportunity to make a broader impact that goes well beyond me.
How did your career progress from your start in 2004 through your current role?
I was just having fun with it and as time went on I started achieving greater success, the initiatives became more sophisticated and we became more confident in taking on new, ambitious initiatives. By 2010 or 2011 we were doing broad-scale lighting retrofits, starting to do sizeable heating and A/C retrofits and exploring solar [energy], among other varying initiatives. At that point, [Chief Executive Officer] Marc Holliday approached me and said, “I really like what you’re doing. I see your passion and the success you’re achieving and we really want someone with your enthusiasm to be able to take this on as a central point person and drive this forward.”
Where does New York City rank in terms of sustainability when compared to other modern cities?
I think New York City is at the leading edge. Other municipalities, particularly in the U.S., are watching what’s going on in New York, whether through private organizations and their efforts, or New York City local laws that have been rolling out, requiring energy audits and upgrades and retro-commissioning and benchmarking. That will have very significant benefits in improving standards here. That said, I still think there is a lot more work to do as technologies continues to emerge and develop.
SL Green has recycled hundreds of thousands of square feet of carpeting and tile. What’s the status on that program?
That’s been a really positive program for us and it carries on today through all of our jobs. We’re able to recycle that material for second-generation products and that’s one of our longest-standing initiatives that I’m proud to say has become a seamless part of how we operate.
If you look at construction in the past, when you would start a job the carpet and ceiling tile were always the first to be removed and they would go into a dumpster and be taken away to a landfill. It’s still the first material to be taken out of the space, but it is broken into its different components and sold back to the manufacturers to make its way back into new products. This is happening on a schedule and cost neutral basis for us.
How many properties have been outfitted with new LED lighting?
By 2012, we had retrofitted about 22 of our suburban and four of our largest New York City properties. In 2013, we continued that effort with another three of our suburban properties and seven of our New York City properties. And this year we are just about to launch forward on nine of our [city] properties.
How do you measure the success of these various initiatives?
We’re always looking at the quantifiable data to understand our metrics and where we’re going. LEED is certainly a very successful program used throughout the industry, but I don’t know if I would say they are sort of the pinnacle achievement of what we are trying to go after. There are so many different metrics that we’re considering, but LEED and Energy Star are very important in their own right to convey to the marketplace what we’re accomplishing.
What does the cost-benefits analysis look like?
Since 2010, we’ve spent about $12.4 million dollars [through 2014] on proactive efficiency measures within the sustainability program. Incentives are a very big part of keeping paybacks within an appropriate range. We’re getting about $3.5 million worth of incentives through state utility incentives and $3.6 million per year in cost savings from efficiencies.
So you’ve recouped that $12.4 million, and beyond?
We paid ourselves back midway through 2012 and now we’re in positive territory.
Do you have any tips for landlords who haven’t yet explored sustainability to get involved?
Always start small and build your sophistication over time. Above all else, whatever technology or program you’re looking to deploy into your assets, it’s about behavioral change. You’re thinking about new ways to do things. So you want to build the confidence that this is something that can work for your company.
In terms of tenant construction work—occupancy sensors, LED exit signs—that’s really about changing a specification on your drawings. Luckily, most of this has become the norm with electricians so it should be an easy transition. And then you can select a new light fixture that’s more efficient. And then you can maybe consider changing out light bulbs in your core and common areas and do a broader lighting retrofit. And then maybe look at heating and a/c with an upgraded automation system, or high-efficiency motors and [variable-frequency drives] on your various building equipment.
In terms of the ceiling tile and carpeting recycling, in many ways the team is historically used to the demolition process and the order in which it happens. Now the only change is that instead of sending it to a dump, you’re sending it to a vendor who collects the materials. That’s an easy change to take on.