How the Construction Industry Can Navigate the Ongoing Supply Chain Crunch
By Barry LePatner September 5, 2022 9:00 am
reprints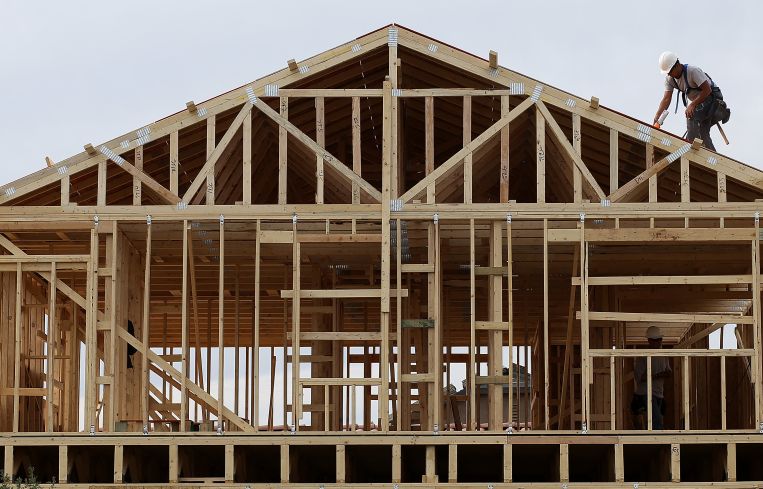
Real estate, design and construction principals eagerly awaiting good news regarding the supply chain or those reliant upon its near-term rebound to smooth operations will need to remain patient. Meanwhile, here are four challenges and a solution for each.
Skilled labor
The COVID-19 pandemic created a shortage of skilled workers, disrupting the construction, repair and revitalization of real estate and infrastructure projects. Over and above its normal pace of hiring in 2022, the U.S. construction industry needs 650,000 additional workers. The enormous backlog created by the pandemic, coupled with the Biden administration’s recent infusion of $1.2 trillion for infrastructure, will compel the industry to find ways to attract — and train — 2.2 million new workers over the next decade.
Owners must secure ironclad assurances from their construction teams that they have the necessary skilled labor to timely complete the full scope of every project. It is entirely appropriate for owners to meet with principals of their general contractor/construction manager and the key subcontractors to secure verbal and written commitments to ensure that skilled labor for key trades are available. In addition, due diligence must be undertaken to ensure that all products and materials specified by the design team can be procured and delivered to the project site so as not to delay the completion date. Get it all in writing!
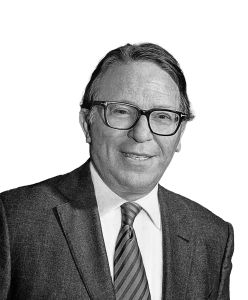
Trucking
The pandemic caused a 70,000-trucker shortfall, slowing the delivery of goods.
Construction principals must have in place a backup plan for unanticipated delays in delivery schedules of products and materials for each project. They should pay particular attention to domestic alternatives for products the architects may have specified that originate overseas. They must also identify alternate delivery routes where driver shortages are reported in a specific part of the nation. Owners must insist on these steps from their contractors and stress that, lacking a backup plan, additional costs for emergency shipping must be borne by the contractors themselves. Again, secure this agreement in writing.
Climate change
The National Oceanic and Atmospheric Administration predicts above-average storm frequency for the seventh year in a row, with the U.S. expected to experience between 12 and 21 named storms through the end of this year. These storms will continue to disrupt and tax an already battered supply chain system. High temperatures in southwest China prompted the government to order industrial power cuts in nearly 20 cities. Factories have shut down or are slowing production as a result, with a cascading impact on exports. In China, a heat wave is causing manufacturers to shut down. Wildfires continue to cause untold damage.
Planned construction projects where the impact of severe climate change has occurred repeatedly will find it increasingly difficult to secure insurance in a market that is restricting coverage. In some states, such as Florida, insurers’ refusal to provide homeowner coverage has forced the state to set up its own insurance fund. Lenders are also factoring in the risks of climate change in determining whether to fund commercial projects. Owners must do their own due diligence when planning a project to identify if these factors may impede their development opportunities. Where the risks are too high, delaying a project may be the best course of action!
Shipping upgrades
The shipping industry was totally unprepared for the pandemic. This created bottlenecks and slowed the loading and unloading of container vessels. When factories ramped up in 2021 to meet the increased and renewed demand for goods, receiving ports were unable to handle the increased volume, leading to further disruption in unloading and reloading cargo vessels. New supply chain problems have cropped up internationally, including potential strikes at ports in Europe that could stall shipments this fall and possibly into the first quarter of 2023.
Owners must make every effort to secure commitments from design and construction teams that products from overseas manufacturers are to be minimized or eliminated wherever possible. Securing “or equals” as alternatives for products that are excessively costly or experiencing delays in shipping is an imperative. Make this a contractual requirement when you interview and retain architects, engineers, contractors and construction managers. Again, have a backup plan ready!
Barry B. LePatner is the founding partner of LePatner & Associates LLP and the author of Too Big to Fall: America’s Failing Infrastructure and the Way Forward and Broken Buildings, Busted Budgets: How to Fix America’s Trillion-Dollar Construction Industry.