New York Developers Figure Out the Electric Building
Costs vary and the work can take a long time — but the pressure's on to shift away from gas
By Rebecca Baird-Remba July 25, 2022 7:00 am
reprints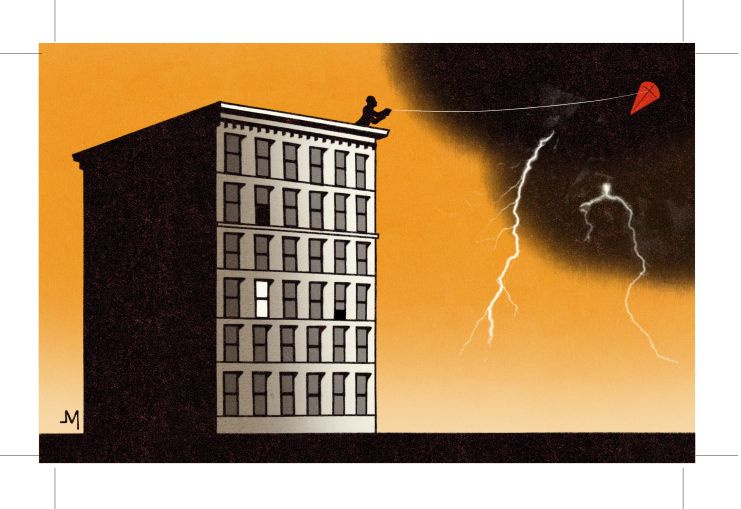
As New York City landlords grapple with official pressure to reduce their carbon footprint, many are wondering how, exactly, they can convert their aging steam heat systems and gas stoves to energy efficient, all-electric options.
The answer isn’t easy, nor the solutions cheap. Costs vary from project to project, but intensive utility work on an entire building can run into the tens of millions of dollars. At the same time, that official — and unofficial — pressure is only increasing.
Developers of new rental buildings know that they have to eliminate gas hookups by 2027, while owners of older properties larger than 25,000 square feet have to start reducing their energy usage beginning in 2024 because of the city’s green buildings law, Local Law 97. Environmental activists are lobbying to ban natural gas hookups in existing apartments, too, and some owners are planning accordingly.
Dramatically changing the heating and cooling system of an occupied apartment building can be difficult, because the work inevitably disrupts tenants’ lives. Even if owners of a steam heat building keep the old steam pipes in place, they still have to remove the radiators, cap the old pipes, and carve holes in the walls of apartments in order to install mini-splits or packaged heat pump units, which provide both heating and cooling. These HVAC systems tend to involve installing chillers — essentially water cooling towers — on the roof, and running new utility lines in the building in order to carry the cooled water to each apartment.
In New York City, smaller landlords have put in ductless mini-splits — which often require boxy metal fan units on the outside of a building — with mixed results. Older heat pumps don’t necessarily heat well in freezing temperatures, and experts argue that landlords in the five boroughs should be installing cold-weather specific units that work well down to -22 degrees Fahrenheit. Tenants stuck with less effective heat pumps then have to rely on inefficient forms of electric heating — like baseboard units or space heaters — to keep warm in the winter.
“Many air source heat pumps, when it gets cold, they start acting like baseboard heaters,” said Pallavi Mantha, an engineer and sustainability consultant at engineering and design firm Arup. “There’s still a lot of work to be done [with heat pumps] and we’re just starting to get there.”
She added that heat pumps work much better when a building is properly insulated. Prewar buildings in New York City — known for leaky double-hung windows and uninsulated brick facades — are not very effective at keeping hot or cold air inside. When a building is tightly insulated, less energy is required to heat and cool it.
“You need to make sure that you have a very tight envelope and that you have very good windows on your building,” Mantha said. “And then you need very little heat to keep your home running.”
She has been working on a major retrofit project for the New York City Housing Authority (NYCHA), which hopes to electrify many of its early- to mid-20th century apartment towers. NYCHA is thinking about attaching new panels to building facades to make them more airtight. This option allows tenants to stay in their apartments during construction, and reduces the need for expensive facade repair projects every decade.
It will involve “prefabricated panels with insulation that gets clipped onto the existing facade. You don’t have to repoint your brick work every so often while increasing the energy efficiency. If NYCHA figures out a solution for their buildings, it will be scalable for lots of other people.”
L+M Fund Management is tackling a similar project at The Heritage, a 600-unit Mitchell-Lama affordable rental building at 1660 Madison Avenue in Harlem. The 1960s complex near Central Park is getting a new facade, and its current baseboard heating system will be replaced with packaged terminal heat pumps.
These units — which resemble their less-efficient cousins, packaged terminal air conditioners (PTACs) — go through the wall and heat and cool spaces using refrigerant, along with backup electric resistance heating for extra cold temperatures. The facade work is also going to involve expanding the window openings, which are narrow for many of the upper floor apartments.
“We’re hopeful that by taking this approach with the facade that we’re retrofitting from the outside in rather than from the inside out,” said Laura Humphrey, the director of sustainability at L+M. “There’s going to be disruptions like any work that’s going on, but we’re hoping this approach will minimize the duration and discomfort that will happen as a result.”
Heather Clark, who oversees building retrofits at RMI, an energy efficiency nonprofit, described the process of repaneling facades as “essentially wrapping the buildings in a sweater.” Much of her work focuses on renovating 1960s-era affordable housing in Massachusetts, where many older brick apartment buildings were never properly insulated.
“So we’re putting a new insulated shell on the outside of the building,” she explained. “That’s able to decrease the load so you don’t have to do much heating and cooling.”
This approach allows contractors to run new utility lines on the outside of the building, which means tenants can stay in the building while construction happens. She also pushes landlords to install energy recovery ventilation systems, which improve indoor air quality by bringing in more outside air. And she encourages owners to trade gas stoves for electric ones, because gas stoves can release carbon dioxide, formaldehyde and other pollutants.
Transitioning from traditional gas stoves to all-electric ranges — whether induction or coil stoves — can be a heavy lift, however. Older buildings may not have the electric capacity to support these kinds of changes, according to engineers. So that may mean new electric lines in the building, a new transformer in the sidewalk outside, and with extra approvals from Con Ed.
“The biggest obstacle is the electrical line requirements for those are high,” said Humphrey. “We have to run new conduit lines — where is that going to go? It’s not off the table, and certainly for deeper retrofits that’s the biggest obstacle. Our tenants pay for their cooking gas. We have to think about the cost and think about equitable cost share.”
The combo of adding new utility lines and repaneling a facade often requires vacating a portion of the building, if not the entire property.
“We have not been able to come up with an easy way to do this in an existing building,” said James Lin, an associate partner at engineering firm JB&B. “Whenever people have asked us about it, it’s highly destructive. You end up having to at least potentially vacate a stack of apartments and come up with some way of retrofitting and getting into those apartments, making the modifications, and then working your way around the building.”
The pandemic has also thrown a wrench into many renovation plans, delaying orders for HVAC equipment built in Europe or Asia by up to a year.
“We’re hearing lead times of 50 or 60 weeks for some air-handling equipment,” said Lin. “I’m hearing, anecdotally, that there have been projects that had promised delivery dates pre-COVID and now can’t even produce a [completion] date.”
New York developers are also competing with European landlords for heat pumps. Although some cities across the pond have adopted the technology, the European Union recently set a goal of 30 million new heat pumps installed in buildings by 2030, in an effort to reduce dependency on Russian natural gas. The United Kingdom has set its own target of installing 600,000 heat pumps per year by 2028, with a goal of banning gas and oil boilers in new homes starting in 2025. Several other European nations have either banned gas boilers in new homes or new gas connections entirely.
Some owners are doing electric retrofits where they can, but leaving gas lines in place for certain uses. On the Upper West Side, Fairstead is revamping a former single-room occupancy hotel on 79th Street into 77 studios for low-income seniors. The gut renovation — dubbed Park 79 — involves new elevators, heat pump installation, and updated apartments with completely new finishes and electric appliances. However, the basement of the 77-unit building was too small for an electric boiler, so the developer opted to keep a gas-fired one.
“The space requirements for the amount of tanks we would need if we were to use an electric boiler was cumbersome from the design side of things,” explained Tyler McIntyre, a managing partner at Fairstead. “We would need to double the amount of tanks because it takes longer to warm up the water.”
New construction, meanwhile, has a much easier path to full electrification. MAG Partners — led by Forest City alum MaryAnne Gilmartin — is working on two all-electric rental projects at 335 Eighth Avenue and 300 East 50th Street. It hopes to get passive house certification—meaning the building will be airtight and highly energy efficient — for the Eighth Avenue project, which will have 200 apartments, including 65 affordable ones.
Alloy Development is also building a major all-electric tower across from Atlantic Terminal in Brooklyn. The 44-story building at 100 Flatbush Avenue will have 445 apartments, 10 percent of which will rent through an affordable housing lottery. It will include an electric boiler, heat pumps and induction stoves.
AJ Pires, the firm’s president, felt that electricity would be “the only way to be powered down the road.
“From our perspective it’s about energy infrastructure,” he said. “Natural gas is going away, and so, at some point, as an existing building, you have to make an investment to change infrastructure. For other people doing new construction, there’s a responsibility to think that way.”
Rebecca Baird-Remba can be reached at rbairdremba@commercialobserver.com.