Andrew Staniforth and MaryAnne Gilmartin Plotting a Modular Empire with Assembly OSM
Andrew Staniforth and MaryAnne Gilmartin first saw the potential for modular construction in Brooklyn years ago. Now, Staniforth, as CEO of Assembly OSM, is taking it to new heights coast to coast.
By Cathy Cunningham January 18, 2022 2:40 pm
reprints
Assembly (n): A group gathered together in one place for a common purpose.
If there’s one thing the past two years have taught us, it’s that just because things were done in a certain way for a long time, it doesn’t necessarily mean the old way was the right way.
The commercial real estate industry has been a sometimes reluctant beneficiary of change and innovation. But, one firm is pushing the boundaries when it comes to an age-old process that was previously, quite literally, set in stone.
Modular construction startup Assembly OSM was founded by Chris Sharples and Bill Sharples, two of the founders of SHoP Architects, in 2019. While the Sharples brothers continue to oversee the company’s strategic direction, Andrew Staniforth took the reins as CEO late last year.
Its mission is clear: Assembly aims to turn the preconceived notion of modular construction on its head through the delivery of architecturally beautiful, high-rise buildings that are greener, cheaper and faster to construct.
The new modular
Think of modular construction and what comes to mind may be stock Lego pieces, put together in an impersonal manner. Right?
Wrong. Just ask MaryAnne Gilmartin, who serves as an adviser to Assembly.
“We don’t want to make people think about prisons and dormitories when we think modular,” Gilmartin, the founder and CEO of MAG Partners, said. “We want to go back to [architect, inventor and futurist] Buckminster Fuller, and recognize that when you have controlled environments, you can deliver unbelievable beauty.
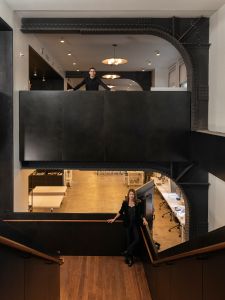
Utilizing the technical know-how of former engineers from the automotive and aeronautics industries, Assembly utilizes cutting-edge technology in every step of its building delivery process, from digital twin manufacturing models — or, real-time virtual representations of the physical construction process — through to eventual on-site installation
Sustainability is a crucial part of its business plan. On the construction front, its buildings have 30 to 40 percent less embodied carbon and a reduction of 60 to 70 percent of on-site emissions. Assembly has also designed its properties to be upgradable and disassembled as markets change, or at the end of their useful life. Further, drawing from a preapproved supply chain allows developers to track the sustainability of each product.
“We feel that attacking this problem from all angles is the only way we will be successful at moving the industry forward,” Staniforth said.
In addition to its eco-friendly approach, Gilmartin said the key void Assembly is filling today centers around innovation.
“It’s a connect-the-dots void,” she said. “As developers, we accept the fact that the way we do things is inherently inefficient, and there has to be a better way. What Assembly is doing is pushing the bounds of that conversation to a place of saying, ‘We can do it better, we can deliver it cheaper, and we can make it beautiful.’ I don’t think that trifecta has been demystified by the development and building community, and I actually don’t think there are many competitors trying to solve that same problem.”
The apartment
As this article was going to press, Staniforth was focused on getting Assembly’s first deal locked down, a 130,000-square-foot multifamily building in Manhattan. Details on the property are still under wraps but — to give eager eyes a taste of what automated architecture can look like — the company put a prototype of a completed one-bedroom unit on display in Harrison, N.J., in late October 2021.
“We’re at a point where what Bill and Chris have built over the last three years at Assembly is now ready to release into the world,” Staniforth said. “Over the last few weeks, we’ve had people come out to our facility in Harrison and see our first units being built. MaryAnne was one of them, and I jokingly said we need one of those roller-coaster flashes that go off when you walk into the unit because everyone’s reaction is, ‘This is amazing,’ because the preconceived notions of modular and prefab just aren’t applicable to that first unit — at all.”
Gilmartin described the apartment as “stunningly beautiful.” She added: “What hit me was the absolute upgrade in every way to the original thought of a ‘modular unit.’ It has evolved significantly in its application to high-end, luxury condominiums, and you can now produce that luxury look and feel at a price point that allows renters at all price points to experience a level of luxury. That’s very, very difficult to achieve presently in construction.”
Assembly buildings are delivered in about half the time and allow developers to reduce both interest and carrying costs, and hold less contingencies, all of which result in an overall less expensive building. Thanks to the cutting-edge technology utilized in their prefabrication, Assembly buildings are also higher quality and more sustainable, making it a win-win for both the developer and the end user.
Technology is the backbone of Assembly, and the company has added engineers from Boeing, SpaceX and Tesla to its team, including Boeing’s former chief technology officer, John Tracy.
Those engineers know how the advanced manufacturing industry has operated most efficiently within the aeronautics and automotive industries, and have helped Assembly implement two fundamental concepts applicable to real estate construction: a single source of product information (or digital twin) and a widely distributed supply chain, where subcomponents — for example bathrooms and kitchens — are manufactured by different suppliers across the country and are ready to roll without delays when it comes time to deliver the building.
Bringing all of these capabilities together, Assembly has also built its own software and combined it with products like Catia, used for computer-aided engineering, and 3D technology so that custom-made buildings can be digitally modeled and manufactured like cars and airplanes have been for decades.
As a developer, “My end of the business is never really going to be on the forefront of innovation,” Gilmartin said. “I think that in some ways this discussion around modular and process innovation and delivering quality in a more efficient way is like a war cry for intelligence in real estate.”
And those who understand the true benefits of that intelligence are the ones who’ve been watching the construction space for a very long time, Gilmartin said.
It started deep in the Forest
Modular construction isn’t a new concept to Gilmartin or Staniforth. In fact, the construction of Brooklyn’s Pacific Park, which included Barclays Center as well as the erection of a high-rise modular tower, was a bonding moment for the two at Forest City when the young Staniforth joined the firm as an intern in 2011, his first job out of the University of Pennsylvania.
On Staniforth’s very first day, Gilmartin handed him a set of plans for Tower B2, now known as 461 Dean Street, the first modular tower next to the arena, and said, “We’re trying to figure this out. Can you take a look at it?” He’d never received a set of plans, let alone looked at anything like it.
“I think that the baptism by fire that we had at Forest City really allowed me to be involved in things that most 20 year olds wouldn’t have exposure to,” he said.
Staniforth wasn’t the only one thrown into the deep end when it came to the project, though.
“None of us had ever built an arena before,” Gilmartin said. “It was about getting the best and the brightest people around the table, including the architects, and figuring out how to do this in a way that was different and lasting. Andrew was a big part of that. The arena process confirmed that he’s a superstar, and then he just needed additional time and exposure.”
Gilmartin described herself as an “episodic mentor” in Staniforth’s career since then, available for counsel when big moments or career opportunities have come his way. Or, from Staniforth’s perspective, “at every pivotal moment.”
A pull toward technology and innovation during his time at Forest City presaged his next move — to urban infrastructure, planning and innovation firm Sidewalk Labs (a subsidiary of Google) — and, after Gilmartin created L&L Mag in 2017, she brought Staniforth over there, where he began working on Terminal Warehouse, the firm’s reimagined former shipping warehouse in West Chelsea. (It should be noted that while Staniforth was working on that project, Commercial Observer named him to its Top Young Professionals in commercial real estate list.)
Staniforth credited Gilmartin with steering him to the places that held learning opportunities. “Sidewalk was a big shift,” he said. “But MaryAnne has always been this force of, ‘Find things that challenge you professionally, and find where you can add value to the industry, to the company, to the ecosystem,’ and for the past 10 years, that’s the way I’ve approached everything.”
Looking back in the context of what Staniforth is now doing at Assembly, Gilmartin described their Forest City modular accomplishments as “important, but not enough. We demonstrated that a building could stand up if 60-plus percent of it was built in a factory — and that’s not an insignificant contribution. What’s now been taken to a much more sophisticated level, is that you can build modules and not sacrifice aesthetics and architecture.
It’s a new dawn
Staniforth’s new role requires many problem-solving skills in an industry resistant to change.
“Understanding the benefits that stem from changing the way that we build buildings — for more affordable housing, and all of the benefits of having a much broader, inclusive workforce who participate in construction — and then being able to keep those benefits at the forefront as you do something that changes the way that stuff has happened for generations is a very clarifying process in terms of what I have to focus on,” he said.
As CEO, his first task was setting a very clear and concrete internal mission at the company. “Once you establish that North Star of values, everything centers around that,” he said.
One of his core leadership philosophies is being transparent with both his team and the broader real estate community to drive home the things for which Assembly stands. Cultivating a diverse and inclusive workforce at every stage of the construction process is one prime example.
“Transparency empowers people to make decisions, and I’m transparent about needing to have a more inclusive workforce and pull different pockets of populations into the construction field, because they’ve been traditionally cut out,” he said. “It’s really important to codify that internally, and then everyone, as they analyze the decisions in their own day, consent around that, and my leadership team doesn’t have to be involved in those decisions. Everyone knows what we’re optimizing for. And that’s part of what I’ve been doing over the past six weeks — getting those concepts just on the table and talking about them very openly.”
One of the big exercises as Assembly grows the team is hiring people that match its values and its mission, and can help it continue to achieve those goals.
Time is money
Developers may take some convincing along the way, but Gilmartin is confident the argument for modular is ready to be made.
“It’s a case of trust and verify in doing these early projects and taking a group of doubting Thomases and converting them,” she said. “You don’t have to be on the higher plane in the world of developers, you can actually be a bit of a lunkhead — and I say that affectionately. As developers we want to get the job done, and make money.”
The benefits should be easy enough for the lunkheads to grasp: Assembly’s building delivery methodology eliminates the potential for human error, shortens project timelines and removes the guesswork from construction costs, thanks to the prefabricated advance pipeline of materials involved.
“We all know that there’s a dire need for housing, and the market is there for it. But as a developer, you don’t know what it’s going to cost,” Gilmartin said. “The innovation that Andrew is working on is going to allow us to be much more certain about cost and time. Time is money and there are so many things that can go wrong when there’s a bigger human factor involved. And I think that this idea that Andrew is going to use the automotive industry and the aeronautics industry to do a better job of delivering for the built environment is something that’s just next level, and beyond anything we were thinking about when we built B2 as a modular building.”
What’s also key — perhaps especially in New York, where buildings’ outward appearances’ are judged like dogs at Crufts — is that design aesthetics won’t be sacrificed along the way.
“The ethos of our company comes from ShoP. And design is so important,” Staniforth said. “At the end of the day, people want to live in places that are beautiful and safe and healthy. When you put that at the forefront of how you approach a manufactured product, you get around some of the preconceived challenges of modular and prefabricated work.”
Breaking down those walls — no pun intended — the company is already in conversations with several of the industry’s starchitects.
“COOKFOX or Norman Foster will be able to design an Assembly building,” Staniforth said, adding that beauty will be one thing that differentiates his firm from others in the modular space. “You don’t have to pick out a building from an assembly line. On the back end, we’ll make it super efficient to execute. But on the front end, it’s going to look beautiful and custom-made with your architect’s stamp on it.”
Staniforth expects Assembly to complete three deals in the next year, likely in New York City and California, where the company has already completed a lot of the pre-approval processes and is ready to rock.
“We started at Forest City with an idea, and it was a hairy, crazy idea that was a jumpstart on this whole idea of doing things better, faster and more progressively in the built environment,” Gilmartin said. “For me, it’s deeply gratifying to see that very early idea turned into something as sophisticated and as promising as what Assembly has put together today.”
Well, that’s pretty OSM.