Health Care Construction as Sustainability Regs Loom: What Works?
A recent Commercial Observer gathered the experts and asked them just that
By Larry Getlen September 20, 2024 9:00 am
reprints
The deadline for filing reports on energy efficiency and greenhouse gas emissions under New York City’s Local Law 97 — or face fines for failing to do so — is coming early next year for most owners of larger buildings. That has significantly impacted those in charge of implementing these standards throughout the health care facilities universe.
This was one clear conclusion to emerge from Commercial Observer’s “Fall Healthcare Construction Forum,” held at the City University of New York Graduate Center on Sept. 18.
After opening remarks from Commercial Observer Editor-in-Chief Max Gross, who discussed the health care sector’s growing prominence within commercial real estate, the morning’s first panel focused on the challenges inherent in managing significant real estate portfolios given Local Law 97.
Emil Martone, director of design and construction at Weill Cornell Medicine, said that their first effort under the new law, a 16-story student residence tower on York Avenue and East 74th Street, will be approached very differently from their formerly cutting-edge LEED Gold research building on East 69th Street, which was designed around 10 years ago.
“It’s all electric, air-source heat pumps, electric hot water, the whole nine yards, and I think we’re good through 2050,” said Martone. “We’re almost approaching a passive house kind of envelope on that building to meet the energy requirements. It’s intense.”
But he also said that the Local Law 97 requirements undeniably present tougher challenges for building owners.
“These are a lot of things you would ultimately be [value engineering] out of projects, but we don’t have that choice anymore,” said Martone. “That makes these projects so much tougher, because cost is ticking up now, but it’s not a discretionary bucket we can attack anymore. So, from an owner standpoint, it makes it tougher to understand where you’re going to get your returns.”
Omer Cabuk, chief decarbonization officer for NYC Health + Hospitals, noted that a decade ago, the organization might use a few million gallons of fuel oil every year. Now, given the utilization of steam traps, pipe insulation, pneumatic controls, unit refurbishing projects, boiler optimization and chiller plants, that number is down to less than 200,000 gallons.
“Over the years, we transitioned from energy efficiency projects to decarbonization,” said Cabuk. “Our bread and butter is still energy efficiency, but we are also preparing our infrastructure for electrification.”
Joseph Mamayek, principal at SGA, talked about his architecture firm’s work on the state-of-the-art research and development facility in Boston known as ISQ3 (Innovation Square 3), which provides 320,000 square feet of life sciences space for Vertex Pharmaceuticals.
“This will be the first building in Boston that will have both a LEED Platinum certification and a LEED Zero Carbon certification,” said Mamayek.
Mamayek said that achieving this required a precise examination of the building’s carbon output.
“You have to look at the total carbon emitted,” said Mamayek. “There are two elements to that equation. First, you have to look at the basis of the energy sources for your building — if it’s electricity, propane, steam, and so on. The other component is the transportation piece, which can only be done once you have users in place for one year. You find out whether they are taking a car, a bike, a water taxi, whatever it is, and that’s your carbon footprint. You have to look at these things in combination.”
The panel also featured Antonio Cabrera, vice president and director of health care at Hunter Roberts Construction Group; Steven J. DiFlora, senior executive director at MG Engineering; and moderator Andrew J. Weinberg, director of business development at LF Driscoll Healthcare.
Next up was a focus on designing for wellness.
“The first step in outstanding and safe patient care is the environment we create for the provider,” said Steven Forti, chief wellness and resiliency officer at the Hospital for Special Surgery.
Forti referred to discussions of light by neuroscientist and podcaster Andrew Huberman, who has noted how imperative it is to have different types of light in the morning and the evening, and how detrimental light designed for morning can be later in the day.
“For people who work a 7 a.m.-to-7 p.m. shift, imagine what that does to their sleepover time, and then imagine how that translates to patient care,” Forti said.
Tina Macica, associate vice president of design and construction for Montefiore Einstein, points out how smart strategies for health care design can emerge from unexpected sources.
“If you go into a spa, you immediately walk into this calming location. Why can’t we take that concept right to the nurses station, then flow it through each of the staff spaces?” said Macica. “Make it so that everything’s a respite space. There are strategies we can use to bring in some softness, and ways to diffuse sound.”
The panel also featured thoughts from Jeffrey Berman, principal at Jeffrey Berman Architect; Rory Creegan, director of HVAC at engineering firm Jaros Baum & Bolles; and moderator Thomas D’Ercole, executive vice president and Northeast regional director for Plaza Construction.
A discussion on collaborative strategies for meeting clinicians’ needs between Roger McClean, director of design and construction, facilities management for Memorial Sloan Kettering, and Elizabeth Sullivan, assistant vice president for architecture at Northwell Health, was followed by a panel on future-ready health care project delivery.
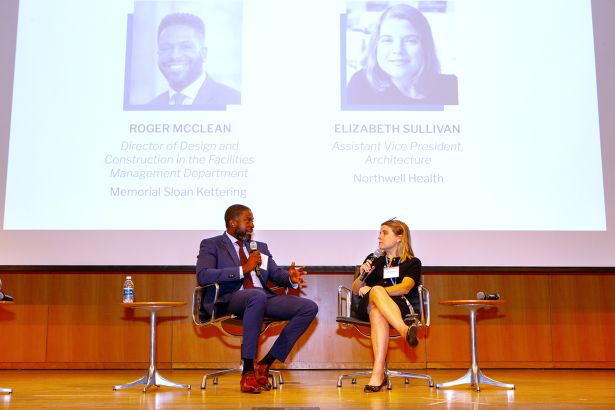
During a discussion on how to achieve optimal outcomes while reining in costs, Vincent Fiorillo, project executive at Consigli Construction, noted that it’s essential to leverage relationships with the subcontractor community, since they are buying the relevant products.
“There are a lot of good alternatives to create a design intent at a lower cost,” said Fiorillo. He described a project he worked on where they were over budget on a facade, and the subcontractor found alternative methods to get the same look at a significantly lower cost.
“I didn’t do that,” said Fiorillo. “We did that with the experts who actually end up buying the product.”
Suzen Heeley, executive director of design and construction for Memorial Sloan Kettering, noted that successful collaboration extends beyond internal teams to include clinical partners whose own enthusiasm can help propel a project forward.
“We use tools like VR [virtual reality], and we recently did a tabletop model for an OR project, and these things really engage people. They get so invested in it,” said Heeley. “They understand it, and their colleagues bring up good points, and there’s just this organic response to these things that really helps them get a sense of what the space could look like.”
Other panel participants included Rob Masters, principal and health practice leader at CannonDesign; Peter Santella, vice president of health care at EJ Electric Installation; and moderator Michelle Augustino, project executive at engineering and design firm VHB.
The day’s final panel focused on the creation of the second Harlem Biospace biotech incubator. It featured Scott Metzner, principal at Janus Property Company; Philip Parisi, associate principal at MG Engineering; Sebastian Quinn, principal at design firm SQBW; Christopher Zelisko, principal at Jack L. Gordon Architects; Gina L. Bolden-Rivera, senior vice president and chief lending officer for the federally established Upper Manhattan Empowerment Zone; and Samuel Sia, the founder of Harlem Biospace II.
Sia said he was especially excited about the opportunity to offer the flexibility of facilities required to truly spark innovation.
“The space we’re growing now in Biospace II is 10,000 square feet of private offices and labs,” said Sia. “It’s the most beautiful lab space I’ve ever been in. There’s a feeling there that it’s not a cookie-cutter type of space, but a very careful design in an area that is unique in the world, right next to Columbia and CUNY. Really offering the flexibility of spaces to support innovation is how you get this economy to grow. We will be an engine like Kendall Square in Cambridge [Mass.] for growing NYC’s bio-economy.”