Brookfield Is Building Manhattan West Using AI
By Rebecca Baird-Remba October 23, 2018 12:00 pm
reprints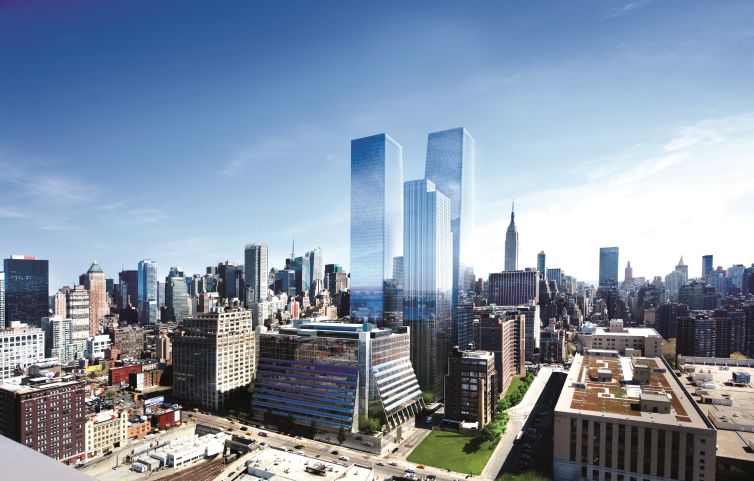
A block away from Penn Station, Brookfield (BN) Properties is constructing Manhattan West, one of the biggest and most complex office projects in New York City. Each morning, roughly 900 workers descend on the eight-acre site on West 33rd Street between Ninth and 10th Avenues—welders, concrete layers, carpenters, electricians—all somehow working in sync to build 6 million square feet of office space.
But how do you keep them all working on time and on budget?
A new tech startup, indus.ai, has created a system to solve the age-old problem of coordinating workers and conveying information on job sites to general contractors. The San Francisco-based firm uses artificial intelligence and cameras to track construction activity in real time, and it has a platform that allows owners and contractors to check in on progress. Project managers can mount cameras on cranes and poles throughout the construction site. The 24-hour video footage is fed into a neural network—a series of algorithms programmed to “learn” like the human brain—that was trained by more than a million construction images and videos to track work patterns, the arrival of materials and how often certain kinds of equipment get used. The firm recently raised $3.7 million in seed financing in a round led by Pierre Omidyar’s venture capital firm UP2398.
At Manhattan West, Brookfield is using indus.ai to monitor how often the construction hoist stops at specific floors and as a result how much time is potentially being wasted because workers have to wait too long to go from one floor to another. The developer topped out the superstructure of the 67-story, 1.8-million-square-foot One Manhattan West tower last month, according to a Brookfield spokesman.
On the site of a typical major commercial high-rise, anywhere from 500 to 1,500 workers file in and out every day, explained indus.ai co-Founder and CEO Matt Man. Many have to wait up to half an hour for the hoist—essentially an open-air elevator that’s suspended on the exterior of a building—which means two-and-a-half hours of lost work time (and tens of thousands of dollars wasted) per week.
“We know how many floors it stops at and how long it spends at each floor,” he said. “So, we can help the general contractor understand how to optimize the methodology of the hoist.”
On average, his firm is able to help contractors reduce the wait time for the construction elevator on their sites by 10 to 20 percent.
They’ve also used their cameras at Manhattan West to monitor the number of people working at any given time, so that contractors can ensure they are following fire and safety codes.
On other sites, Man’s tech can analyze how long it takes to build one floor of a high-rise. Then it uses that data to track structural progress and notifies project managers when construction starts to fall behind, so that they can fix delays before they derail a development.
The construction and development company Skanska employed indus.ai to monitor the construction of a dorm at the University of California campus in San Francisco. Executives from the university and from Skanska could see, remotely, whether workers were showing up on time, whether Skanska was receiving the correct number of deliveries, and get a bird’s eye view of the project that enabled them to step in when work seemed to be slowing down. (The company didn’t immediately respond to a request for comment.)